
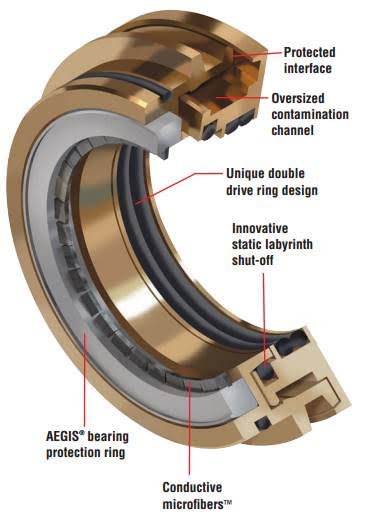
Except for brief time periods when the gap mayīe bridged by an oil film, this air gap is large enough to allow the continual exchange or inflow-outflow of atmospheric air with its ever-present contaminants, primarily water vapor and air-borne dust. In essence, an air gap separates the rotating and stationary elements.
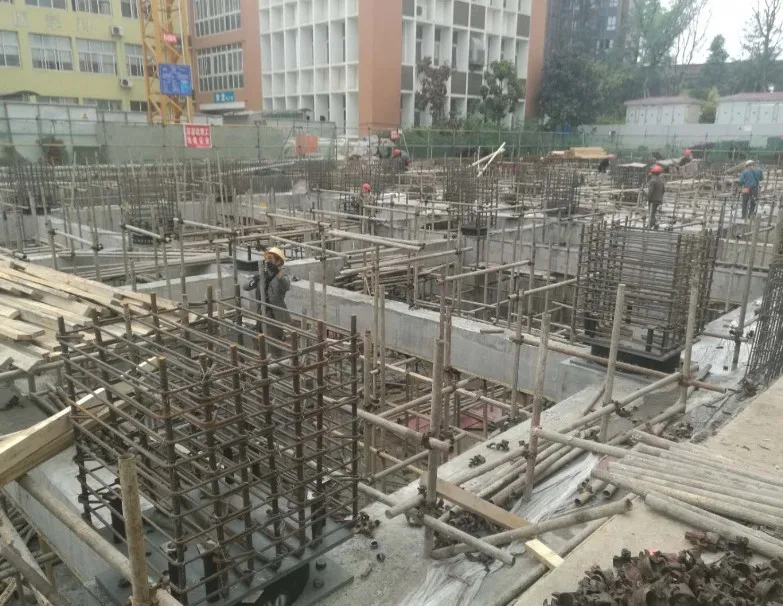
It should be noted that these rotating devices are designed with inherent clearances. Isolators or bearing protectors, for short. Institute standard API610 11 th Edition (section 6.10.2.6)Īs a consequence of these findings and in an effort to reduce the pressure-related alternating in-and-out flow of contaminated ambient air, conventional labyrinths are often replaced by rotating labyrinth seals, which are often called bearing

Lip seals do not meet the requirement of IEEE standard 841-2001 for electric motors or American Petroleum Today however it is generally accepted that lip seals have limitations, but due to inexpensive initial cost they continue to be widely applied. Rubbing, lip seals can’t fully protect the bearing from moisture or particle ingress, which ultimately results in bearing failure. This surface contact often results in costly damage to the shaft itself (left). They rely on surface contact between the seal lip and the shaft to form the seal. Historically the most common way of protecting bearings was The laws of physics are at work here.The image on the right Illustrates the consequences of this contamination. Temperatures cause pressures to go up, while decreasing temperatures cause pressures to decrease. With increasing temperatures, the vapors floating above the liquid oil level will expand with decreasing temperatures the vapors will contract. Nighttime, and temperatures differ when operating versus non-operating. Also, bearing housings undergo temperature shifts from daytime to Way into bearing housings through openings where equipment shafts protrude through bearing housings, or at vents and breathers provided somewhere on the oil-lubricated assembly. Research and follow-up analysis by bearing producers and users has established lubricant contamination as the predominant failure cause (see chart above). It has long been recognized that as many as 91% of all the rolling element bearings installed in the world’s machinery fall short of reaching the manufacturer’s calculatedĬauses of Bearing Failure Lubricant contamination Bloch has written 18 books and over 480 technical papers on practical machine management, reliability engineering, oil mist This article was written by Heinz P Bloch, mechanical engineering authority, consultant and author.
